Why the job isn’t done on post-Covid supply resilience
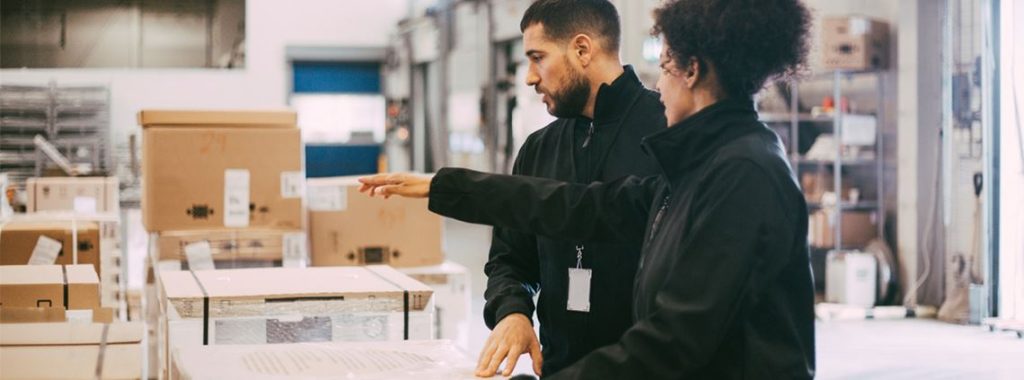
Supply is at a “critical” point and supply chain leaders must “finish the job” to ensure resilience.
New research by consulting firm McKinsey found 92% of supply chain leaders had changed supply chain footprints to boost resilience in the last year, but the report warned businesses have only “partly addressed” underlying weaknesses in supply chains.
The report, How Covid-19 is reshaping supply chains, said: “Companies have only partly addressed the weaknesses in global supply chains exposed by the coronavirus pandemic. In the face of new challenges, finishing the job is even more urgent.”
The report added: “The coming months could turn out to be critical for supply-chain leaders.” It said while some companies would build upon the momentum they gained during the pandemic, others “may slip back, reverting to old ways of working that leave them struggling to compete with their more agile competitors on cost or service, and still vulnerable to shocks and disruptions”.
These are the ways Covid-19 changed supply chains:
1. Inventories and regionalisation
The survey found 61% of businesses increased their inventories of critical products throughout the past 12 months. This was more than had expected to do so – in a McKinsey survey of supply chain leaders last year, only 47% said they planned to increase inventory.
The research noted structural differences between sectors allowed for different approaches to build resilience within supply chains. It described the healthcare sector as “resilience leaders” following efforts to source PPE, and it found 60% of healthcare respondents said they had regionalised their supply chains and 33% ssid they had moved production closer to their end markets.
It found only 22% of automotive, aerospace, and defense businesses had regionalised their production, even though more than three-quarters of these had said in 2020 this was a priority.
Meanwhile, chemicals and commodity players made the smallest overall changes to their supply-chain footprints during the past year. It noted this was because chemical and metals sectors are asset-intensive sectors with large and expensive production sites, where investments in new capacity can take years to complete.
It found almost 90% of businesses said they are looking to increase their regionalisation over the next three years.
2. Risk management
The report said: “The pandemic pushed risk to the top of virtually every corporate agenda,” adding for the first time 95% of businesses now have a risk management process.
An additional 59% of companies said they had adopted new supply chain risk management practices over the past 12 months, and only 4% had set up risk management systems from scratch.
While the report praised businesses for taking these steps, “significant blind spots remain in most companies’ supply chain risk management setups”.
Only 2% of companies understood the location and risk faced by their tier three suppliers and beyond. The report said these gaps in transparency and information were important “because many of today’s most pressing supply shortages, such as semiconductors, happen in these deeper supply chain tiers”.
In fact, 11% of respondents said they had no visibility into their supply chains.
3. Technology and organisation
71% of respondents said following recent supply chain disruptions, they were ramping up the use of analytics to help in advance planning. Additionally, an overwhelming majority of survey respondents said they had invested in digital supply chain technologies during the past year, with most investing more than they originally planned.
The report said: “The benefits of advanced analytics in supply chain management are now being recognised across industries. With the sole exception of the healthcare sector, more than 50% of respondents in every industry say they have implemented additional analytics approaches during the past 12 months.”
Specifically, since May 2020, 30% of respondents said they had introduced digital performance-management systems – which the report called “an important enabler of supply chain visibility – and just under half of respondents said they were looking at introducing network-modelling tools to help improve the long-term outlook of supply chains.
Almost every company also planned for further digital investment in the future.
The report said: “Today’s ongoing and planned digitisation efforts are most likely to focus on visibility, as companies strive for a better picture of their supply chains’ real-time performance.”